Decarbonizing the Aluminum Industry
Last October, I considered low-carbon steel with hydrogen reduction as opposed to the conventional carbon reduction. Steel is one of the major industries of concern for emissions; the others of the big five include aluminum, cement, paper, and chemicals (especially plastics). Aluminum is the topic of today’s post. I hope to cover the other three someday. I will focus on inert anodes for aluminum electrolysis—what this means and why it is important—and touch more lightly on other aspects of the industry.
The Modern Aluminum Industry
Aluminum, or aluminium for British readers, is the third most common element in the Earth’s crust at over 8%, but until recently, isolated aluminum was scarce and expensive. According to (possibly apocryphal) legend, French Emperor Napoleon III would reserve aluminum dining utensils for the most honored guests at banquets, leaving gold utensils as the second tier. The Washington Monument was crowned with an aluminum cap; at the time, the cost of an ounce of aluminum was roughly equal to a day’s wages for a worker on the Monument. Today, the cost of an ounce of aluminum is roughly 17 seconds of wages of someone making $15 an hour.
Credit for the first isolation of aluminum is given either to the Danish chemist Hans Christian Ørsted in 1825 or the German chemist Friedrich Wöhler in 1827. An 1854 improvement of Wöhler’s process by the French chemist Henri Étienne Sainte-Claire Deville, and the Deville process in 1859 to produce alumina from bauxite ore, turned aluminum into an industrial material, albeit an expensive material. Further improvements were achieved by the Belgian electrical engineer Zénobe Gramme.
However, the real breakthrough occurred on two occasions in 1886, when the American engineer Charles Martin Hall and the French engineer Paul Héroult independently developed what is now known as the Hall-Héroult process. The process electrolyzes alumina (Al2O3) in cryolite (Na3AlF6) and produces nearly pure aluminum. The Hall-Héroult process remains to predominant method of aluminum smelting to this day.
Alumina, or aluminum oxide, also doesn’t come from nature for free; it must be refined from bauxite ore, and this is done through the Bayer process, invented in 1888 by Carl Josef Bayer. The Bayer process is also used to this day.
World aluminum production was over 70 million tons in 2023, with a market size of $150 billion in 2021, and is projected to exceed 107 million tons per year by 2050. Aluminum is used widely in the modern economy for packaging, vehicle bodies, common personal objects such as utensils, coins, and many other purposes. Valuable properties of aluminum include corrosion-resistance and a high strength/weight ratio. As of 2022, greenhouse gas emissions were the equivalent of 15.1 tons of carbon dioxide for every ton of aluminum, or about 1.1 billion tons. This is around 2.5% of world greenhouse gas emissions. Here is an overview video of the Bayer process, one of the Hall-Héroult process, and one of the casting of aluminum.
With the background covered, let us review the major steps of the aluminum lifecycle to understand how decarbonization might work.
Mining
According to the International Aluminum Institute, mining is the least carbon-intensive step of aluminum production at less than 0.3% of total lifecycle emissions.
The main source of aluminum is bauxite ore, which contains the aluminum hydroxide minerals gibbsite, boehmite, and diaspore. Bauxite is a mineral that has been flagged for worries about supply availability, though history has shown that supply shortages very seldom materialize as feared. Kaolin, a clay mineral, is another usable source of aluminum. Bauxite mining poses many of the same environmental hazards as other forms of mining, such as air, water, and soil pollution; leaching into the water supply; and health concerns.
The residue from bauxite after refining alumina is called red mud, and it could be a valuable source of iron. Mining produces 1.2 tons of bauxite residue for every ton of alumina. Red mud is mostly stored in a bauxite residue storage facility; this report from the International Aluminum Association describes secondary uses for red mud and also the most responsible methods to manage it.
The Bayer Process
According to the IAI again, refining is the second most greenhouse gas-intensive step of aluminum production, comprising ~17% of lifecycle emissions. Of those, about two-thirds are from process heat. Here’s a schematic of the Bayer process.
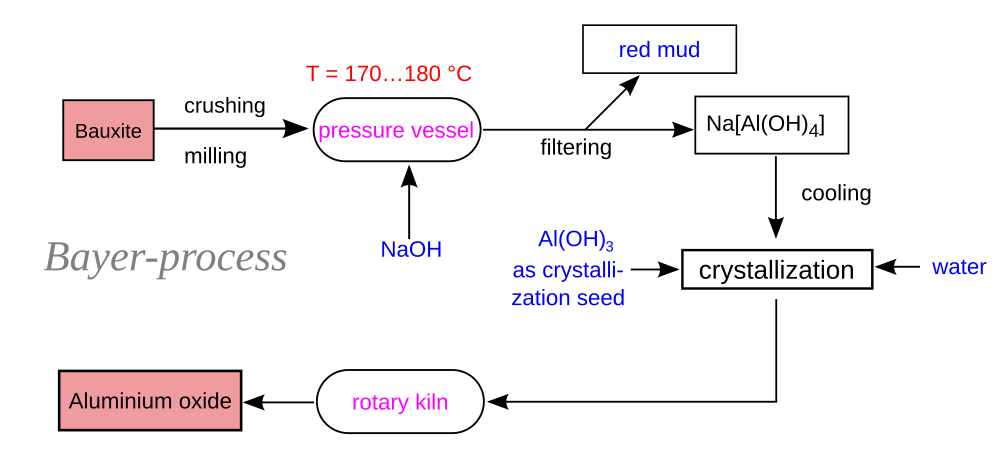
About half of the process heat in the Bayer process is at a low temperature, up to 280 °C (low temperature by industrial heat standards), while the other half is a calcination process with temperature up to 1150 °C. The Australian Renewable Energy Agency is exploring solar thermal for the low temperature portion. Unfortunately, there does not yet exist a promising solution for high temperature process heat. Direct electrification and green hydrogen are two possibilities. As of 2021, the sources of industrial heat (high and low temperature) included 45% coal, 30% natural gas, 15% oil, and 9% renewables (percentages do not add up to 100% due to rounding). This would be a good topic for another day.
Inert Anodes
According to the IAI, 10% of aluminum’s greenhouse gas emissions are process emissions from electrolysis, and another 5-6% are perfluorocarbon emissions that also result from electrolysis. I’ll explain what that’s about shortly.
But first, the process emissions. Anodes used in aluminum electrolysis are made of carbon—graphite to be precise. Since electrolysis strips aluminum and oxygen bonds in the alumina, a carbon anode reacts with free oxygen and forms carbon dioxide: 380-450 kilograms of carbon are consumed for every ton of aluminum by this mechanism, which means that the Hall-Héroult process produces more carbon dioxide than aluminum by mass. A biomass-based anode is one option for a carbon-neutral reaction, but of greater interest is an inert anode, which means that the material does not react at all. To tell you the truth, I don’t understand the reasons that carbon anodes are favored today, and I would be grateful if someone knowledgeable of the industry would chime in.
The idea of an inert anode is hardly new, and unsuccessful efforts to develop one go back to Charles Hall himself. But over a century later, this has proven to be a particularly thorny research and development problem. Candidate materials include various metals, ceramics, and cermets (metal-ceramic composites). The main challenge is developing a material that can withstand the 950 °C temperature of electrolysis, that does not corrode or dissolve in the electrolyte, and that has the necessary conducting or semiconducting properties. As an added bonus, the oxygen that does not react with the inert anode can be a salable coproduct.
The two leading efforts to commercialize inert anodes are from Elysis, a consortium of Alcoa and Rio Tinto with support from Apple, and from the Russian aluminum smelter UC Rusal. As of 2022, Elysis had hoped to conduct demonstration projects over the following two years and begin with full-scale installations this year. Rio Tinto gained a demonstration license at a plant in Québec last month. “I’ll believe it when I see it” is always the right stance for commercialization of a new technology, but in this case, I am optimistic that inert anodes are finally happening after more than a century of pursuing the holy grail.
As mentioned above, perfluorocarbons, particularly carbon tetrafluoride (CF4) and hexafluoroethane (C2F6), are also unwanted byproducts of aluminum electrolysis. These gases are the result of the anode effect, with a technical explanation here. CF4 and C2F6 respectively induce 6500 and 9200 times the 100-year global warming potential as carbon dioxide on a per-ton basis. An inert anode would also eliminate PFC generation.
Electrolysis
According to the IAI, nearly 60% of aluminum’s emissions are due to electricity for electrolysis. These emissions are largely beyond the control of the aluminum industry and depend on the carbon intensity of the electric grid. I’ve written about decarbonizing electricity many times before and will not do so again today. However, the one thing that is within the industry’s control is the energy efficiency of electrolysis.
An inert anode will, by itself, probably not bring about energy efficiency, and it may even require more energy. For one thing, the carbon-oxygen reaction with a carbon anode is exothermic, and so this offsets some of the energy that electrolysis requires. For another thing, the decomposition voltage with an inert anode increases, which means more electricity is required.
An analysis by Ian Wells and Sophia Ahmed at the NRDC states that the theoretical minimum energy of the Hall-Héroult process is 5.99 kWh per ton of aluminum with a carbon anode, and it is 9.03 kWh/ton with an inert anode. Actual energy required is 15.37 kWh/ton, well above either theoretical minimum. An analysis by SINTEF argues that in general, we should expect an inert anode to add ~3 kWh/ton to the energy requirements, with the result that the carbon savings from the anode will be eaten up by the upstream emissions of electricity if the electricity comes primarily from fossil fuels.
I don’t think this is right, though, especially if the inert anode is paired with another sought-after innovation: the wettable cathode. A wettable cathode would allow a shorter distance between the anode and cathode, thereby reducing the voltage drop and the energy requirement. The energy savings might be as high as 25%. Like inert anodes, wettable cathodes are a difficult and long-standing R&D problem, but unlike inert anodes, I am not aware of any advanced pilot projects today. The leading candidate is a titanium diboride composite.
One more thing to briefly mention is the alternative chloride process, which converts alumina into aluminum chloride (AlCl3), which is then electrolyzed. Energy requirements are 25-30% lower. Carbon dioxide emissions are moved from electrolysis to the carbochlorination stage, from which carbon capture is easier due to higher CO2 concentration. SINTEF has an analysis. The chloride process is something that Alcoa pursued heavily from the 1960s to the 1980s, and it is not the exciting idea in the industry that inert anodes are, but sometimes it is worth trying with fresh eyes ideas that didn’t work out in the past.
Casting
According to the IAI, casting constitutes less than 1% of the emissions of the whole aluminum smelting process. The main source of emissions is process heat, and comments made above in the context of the Bayer process apply here too.
Recycling
Due to its high value, aluminum is one of the most well-recycled commodities. Recasting scrap aluminum has 5% of the energy requirements of manufacturing from virgin sources, and so on a per-ton basis, the environmental benefits of recycling dwarf anything else discussed here. About a third of aluminum produced today is from scrap, and that figure could reach a half by 2050.
There are ways to increase the recycling rates of aluminum cans, as described here. The same article discusses the failure of scrapyards to properly utilize aluminum recovered from cars, and how that might be addressed. The IAI argues that a global 71% recycling rate of aluminum cans can be achieved, which would save 60 million tons of CO2 per year, or about 0.15% of world emissions.
Material Efficiency
Can we use less aluminum without deprivation? According to a 2019 report from the International Energy Agency, yes we can, and 17% less to be precise. This comes from things such as lightweighting of vehicles.
Andrew McAfee documents in More From Less: The Surprising Story of How We Learned to Prosper Using Fewer Resources―and What Happens Next that various forms of material efficiency is a central pillar of innovation. This paper finds a 77% rebound effect from material efficiency (in general, not just aluminum), meaning that of the emissions savings from material efficiency, 77% return as increased demand and economic growth. Material efficiency is thus particularly good at spurring economic growth. But the converse is that material efficiency is not particularly efficient at reducing emissions. At any rate, it is not clear to me what policies would spur material efficiency other than general things like economy-wide carbon pricing.
Conclusion
As we have seen, there are many possibilities for improving the environmental performance of aluminum. However, most solutions—particularly low-carbon electricity and process heat, recycling, and material efficiency—are beyond the control of the industry itself. The aluminum industry’s most impactful option is to develop and deploy inert anodes and wettable cathodes, with perhaps the chloride process as a wild card.
On Urban Cruise Ship, I have written a less wordy and more number-y analysis arguing that with either a modest carbon valuation and/or a reasonable expectation of operational savings from inert anodes, it should be beneficial on net to deploy the technology.
Charles Kenny of the Center for Global Development has proposed an international sectoral agreement to phase out the trade of carbon anodes, modeled after the Kigali Amendment to the Montreal Protocol to reduce hydrofluorocarbons (potent greenhouse gases used as e.g. refrigerants). The proposal is premature, in that inert anodes have not yet been commercially proven, as optimistic as we might be. In they are, such a proposal may be superfluous, in that it would at best accelerate a trend that would be driven by market forces, or it may force a transition that would otherwise not occur. The proposal is a good illustration, though, of sectoral agreements where broad carbon pricing has not been feasible.
In the end, I think aluminum is a good illustration of how friendliness to innovation is the best solution to environmental problems. Aluminum is essential to the modern world, and doing without is not a reasonable option. Aluminum will also play a critical role in such environmentally necessary technologies as solar panels and electric vehicles. A broad-based carbon price would help, but new technology is the only way forward.
Quick Hits
Alex Trembath and Seaver Wang at the Breakthrough Institute wrote about the three pillars approach to green hydrogen subsidies, arguing that the framework is too stringent and should prioritize building a thriving hydrogen electrolysis market over immediate emissions reductions. I’m not so sure that green hydrogen production should be subsidized at all, but insofar as it should, I think their analysis is good.
John Cochrane (the Grumpy Economist) wrote a three-part series comparing Kamala Harris’ recent price gouging proposals to the price control policies of the Roman Emperor Diocletian.
The Committee for a Responsible Federal Budget prepared a decidedly less humorous analysis of Harris’ economic policies, arguing that they would add $1.7 to $2 trillion to the deficit over a decade. The proposals are not all bad—the expanded Child Tax Credit in particular is welcome—but overall the proposals show more political than economic sense. The housing subsidies are especially galling. Subsidizing home ownership without addressing zoning regulations is like putting one’s foot on the car’s accelerator while the parking brake is engaged; one will burn fuel and not go anywhere.
This rather critical analysis of the CHIPS and Science Act by Rob L'Heureux argues that the legislation will provide a one-time sugar boost to American semiconductor manufacturing, but it will do little to establish long-term American leadership. I think I’ve mentioned before that I recently took a job at a semiconductor manufacturing firm as a fab tech. We have not (yet) received any CHIPS money, but it is plausible that money from the bill sent an industry signal that helped me get this job. But I still think the CHIPS and Science Act was bad policy.